Cordless drills seem commonplace, but it wasn’t long ago when most drills available were only A/C powered corded models. The current crop of pro-grade cordless drill/drivers offer as much power as corded models, as well as all-day runtime. Advancements in battery technology and electronics continue to increase power and performance, and the basic mechanics behind how a drill works has dramatically changed.
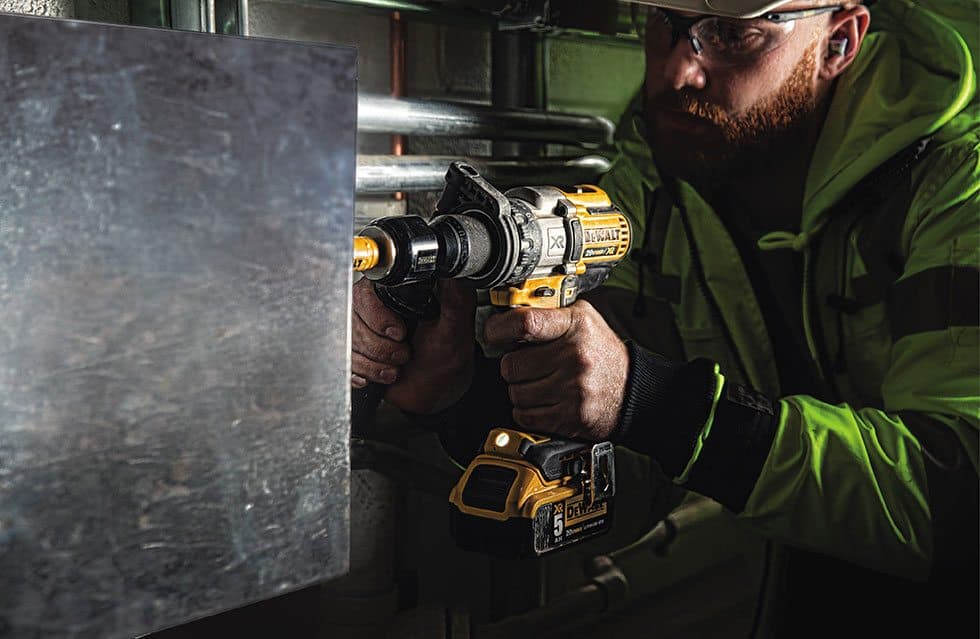
We asked Bill Gallagher of Stanley Black & Decker, to help explain how a drill works. He’s the Director of Engineering for Drilling and Vertical Fastening, so if anyone knows the ins and outs of a drill it’s him. Bill is innovating at the cutting edge of cordless tool technology. with Dewalt (which is part of the Stanley Black & Decker family) They have been pushing the boundaries of battery and tool technology with the introduction of the Flexvolt tool platform and the first ever cordless table saw and 12-inch miter saw.
Basically, drills convert electrical energy into rotational torque to drill holes, tap threads, and tighten/loosen fasteners or any application that needs rotation.
For lithium-ion battery powered cordless drills, the process goes a step further where the tool must have the smarts to actively manage battery health and user safety. A chemical reaction within a lithium-ion battery produces voltage across a positive and negative portion of the battery. Several batteries are stacked in a row, series and parallel connected. This is done to boost the voltage and current that the motor will need to produce high torque and RPM.
There are sophisticated electronics that are programmed to monitor battery condition, both before the drill starts running and during operation. It looks at things like battery voltage, voltage differences between cells, temperature, current being supplied by the entire pack, and more. It must monitor these conditions to protect the cells during operation to ensure safety and battery longevity.
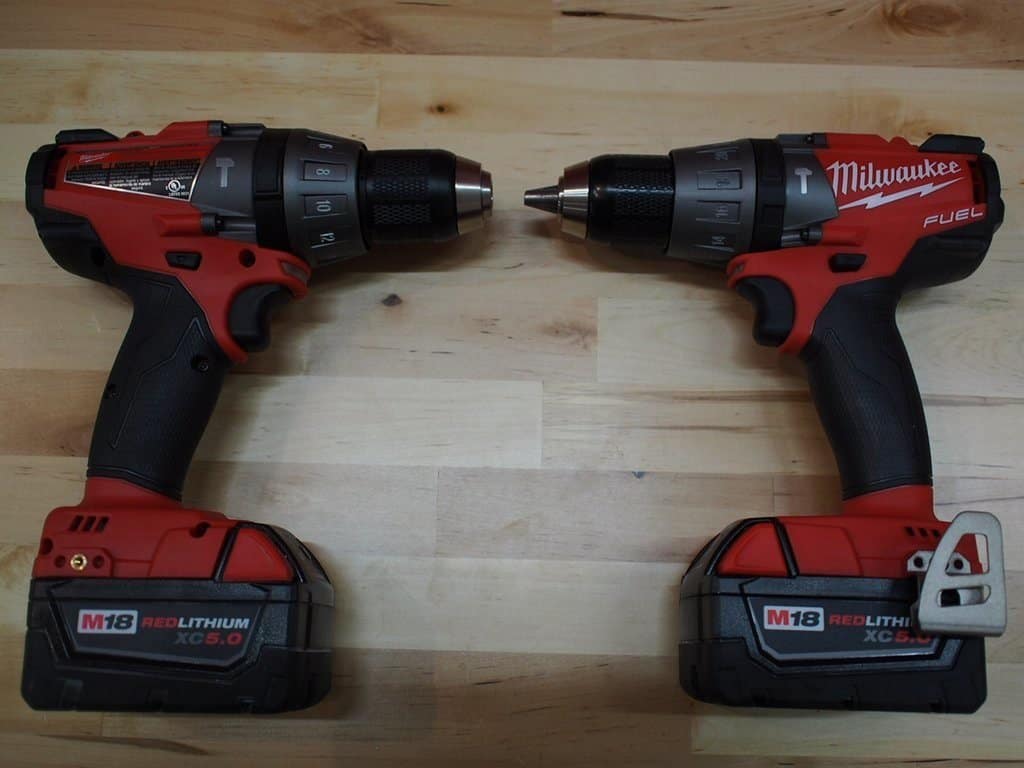
From there, the power is regulated by the user’s trigger finger, pushing the trigger deeper into the handle will signal the electronics to supply more voltage, or pulse width modulate (PWM) the voltage to feed the motor and to change motor RPM. The electrical power has now has been transformed into rotational power.
From there, the power enters a transmission, usually a planetary gear type, that typically has either 2 or 3 selectable gear ratios or speeds. The different gear ratios are to provide different speed/torque ranges for various applications. For example, large self-feed bits into wood or hole saws require high torque and low speed while small twist bits in metal or other materials require low torque and high speed to get the job done.
The power then flows through the chuck, which is a device that firmly grasps the accessory to bore the hole or drive the screw. The chuck, typically, has three “jaws” that clamp down on a round or hex shank of the accessory to transfer the rotational torque. The jaws clamp with hundreds of pounds of force to ensure that they don’t slip on the accessory. Tightening the chuck is performed either by use of “key” that is a bevel gear arrangement that rotates the chuck outer sleeve or simply by gripping and rotating the outer sleeve of a “keyless” chuck. Internally, there are threads that are connected to the chuck outer sleeve that mate with threads on the jaws that translates sleeve rotation into an axial jaw movement. This moves the jaws forward and inward on a slight angle, like a wedge, and clamps down on the accessory.
Once you’ve attached your bit you are ready to begin drilling or driving.